Our customers
Power in Numbers
There are at least a couple groups of theaters running CCI gear that have formed loose collectives to share the CCI gear that they own with each other. If one theater needs a piece of gear and another theater has it to lend, everyone wins.
One group is in Southern California and members include San Diego State, Old Globe Theatre, Southcoast Rep, and Cal State Fullerton. The other group is in the Seattle area and includes the Village Theatre, A Contemporary Theater, and Seattle Pacific University.
The benefits are enormous
If you need to supplement your own inventory for a big show, there’s always a good chance you can borrow from the theaters around you instead of investing in equipment that you might not need again. We’ve even heard stories of these groups moving beyond automation and sharing other kinds of equipment through the same email lists. It’s nice to know our gear can bring people together!
Virtual Inventory – Real Help
In the next couple of months, we’re going to look at the map and see if there are other areas that fit this pattern and work to put people in touch with each other. It doesn’t need to be big; even two theaters can each have a much bigger ‘virtual’ inventory.
If you’re interested in being a part of something like this, drop me a line at peter@creativeconners.com and we’ll find out where the nearest CCI gear is to you. Sharing is good.
Uncategorized, USITT
Time to Teach Some Tech
Gareth and I will be attending USITT in Milwaukee later this week and Gareth will be a presenter at “Turntables on a Budget” Thursday at 1:00. If you’re going to be at USITT and want to meet up, drop me a line at ian@creativeconners.com. Always great to meet our customers face-to-face!
Machinery
We Do Window Displays (at least the automation)
Last year we did a custom job for Cigar Box Studios for their window display at the Ted Baker store in Manhattan. We made 4 custom linear actuators that came out great and have been running non-stop for about 8 months.
Shop Test
Yesterday we found this video of the shop test:
Our actuators handle the items that are traveling up and down. Here’s a video that we posted to YouTube last year showing the actuator being tested before going to New York:
These actuators are for sale, so let us know if you’re interested in getting a couple for your theatre!
Machinery, Tips
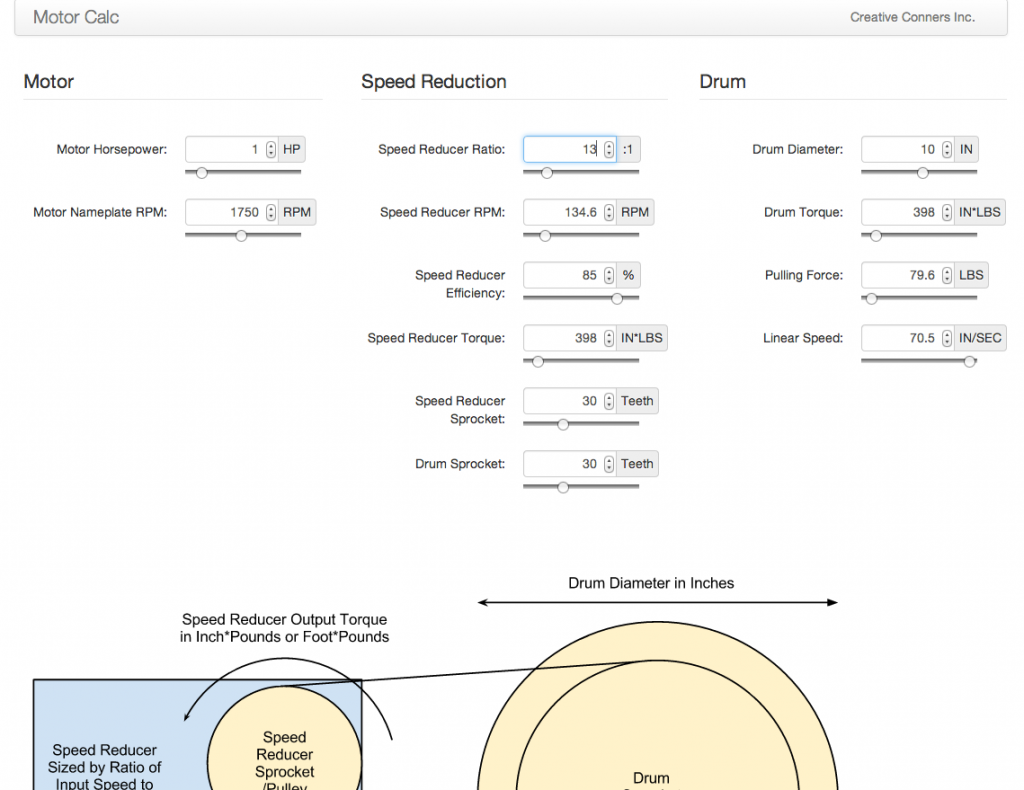
Motor Specifier Tool
Big news today! Over the last week or so, Gareth has been putting together a sweet calculator for figuring out all of your gearing and capacities when designing machines. We’re calling it ‘Motor Calc’ and it just went live at http://motorcalc.creativeconners.com. Please check it out and let us know what you think. Motor Calc works best in Webkit-enabled browsers like Chrome and Safari.
Creative Conners Business, Hardware, Machinery
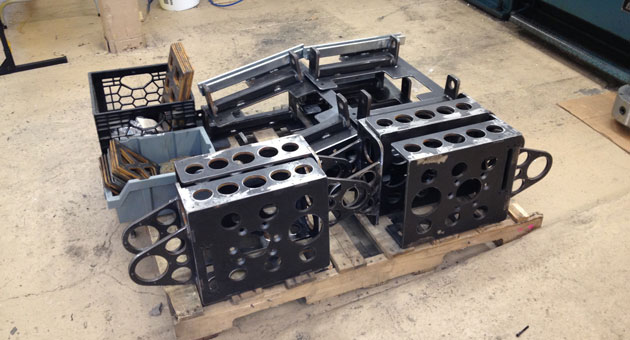
Weekly Update – PARTS Incoming!
Here’s what 5 Revolver frames look like before they head off to powder-coating. There’s also some deck sheaves in there.
Creative Conners Business
One of my New Year’s resolutions is to do a better job marketing our products. Five and a half years ago I was much more aggressive about sending out brochures and postcards regularly. Of course, back then we weren’t really making any sales so I had plenty of time on my hands to focus on marketing.
Those efforts slowed to a trickle as production demands grew. Last year we sent out a single mailing in January and then nothing else. I think it’s dangerous to get complacent about growing our customer base.
As an experiment, we are going to send out a direct mailing once a month for the entire year and track the resulting interest and sales to determine how much our marketing efforts are worth. To liven up the experience, we’re rolling out 3 promotions during the course of the year that will be announced on postcards and on our site. So get ready, it’s going to be a fun year!
Automation, Programming
Just a quick post to point out a cool new feature in SpikeMark — Input Actions.
Before Christmas, one of our customers had a specific need. They do a lot of performer flying systems and build incredibly complex cue link sequences to achieve realistic flying effects. Sometimes a winch needs to be temporarily removed from the show for a cue or two. If a performer misses a pickup, the motor needs to be disabled and the automation tech will drive the winch manually to get the actor back on spike. They have built their own hardware to make it easy to switch between automated control and joystick control, but SpikeMark wasn’t playing nice.
In an automated cue link sequence, SpikeMark wants to see every motor involved in the cue load the cue information before executing. This is obviously done for safety, if the cue isn’t fully loaded SpikeMark doesn’t want to crash scenery. In the performer flying scenario, the operator KNOWS that it’s OK to run the cue sequence, in fact disrupting the link sequence causes a lot of trouble. What was needed was a button that could be pressed to temporarily deactivate a motor and let the rest of the show carry on as if it didn’t exist. So… what to do…
Just after Christmas, another customer had a show with a triple ring turntable. Each ring would be running in a cue and at an actor-driven moment in the show, the middle ring needs to decelerate and stop. If you tried to use “Stop All Cues”, all 3 rings would stop. The stop point is actor driven, so there’s no way to write an automated link. What was needed was a button that could be pressed to abort a single motor out of a cue sequence.
So.. what to do…
A new feature called Input Actions
If you have a Stagehand FX, you can now use the inputs to trigger global actions. The first two actions that have been created are:
Deactivate Stagehand
This action will take a motor out of all cues until the input is released without affecting cue links.
Soft Stop Stagehand
This action will abort a Stagehand by taking the programmed deceleration rate immediately without effecting other motors running in a cue.
Input Actions can be added to any FX input and multiple actions can be attached to a single input, making some cool effects possible. Below is a screenshot:
If you have ideas for more Input Actions, let us know because I’d love to make this feature even more useful.